設計課 Iさん インタビュー
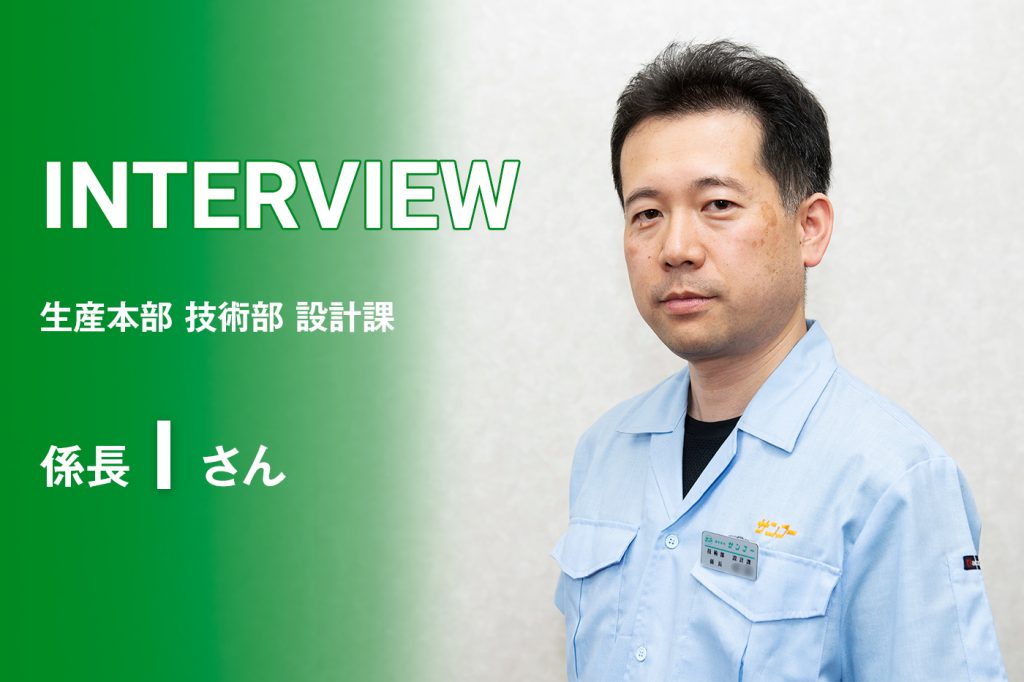
技術部設計課では、デジタルカメラなどの電子機器や自動車に使用されるプレス部品、およびにプラスチック部品をつくるのに必要な金型の設計をしています。それが全ての大元になるものです。精密部品のような細かいものから自動車部品のように大きなものまで各分野におけるプレス加工を手がけているので、全てにおいて対応できるのがサンコーの強み。基本的にはお客さまからいただいた2次元の図面、もしくは3Dのデータを基に、それをつくるのにどのような金型を設計すればいいのかを考案して具体化していきます。
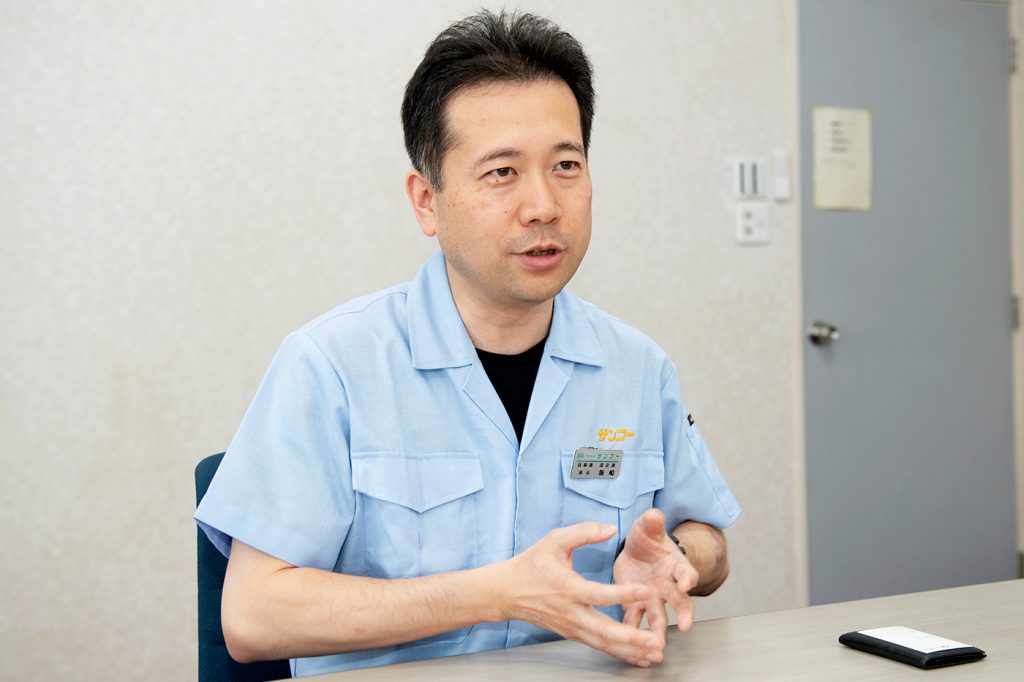
近年は受注する部品の形状がかなり複雑になっている場合も多々あります。従来なら2部品で形成されていたものが1部品になっていたりとか、様々なものが複合したりしているパターンも。それに対応する金型をどうつくるのかが課題となっており、工法で悩む部分もあるのも事実です。その場合は、開発部にも知恵を借りながら金型製作を進めていきます。
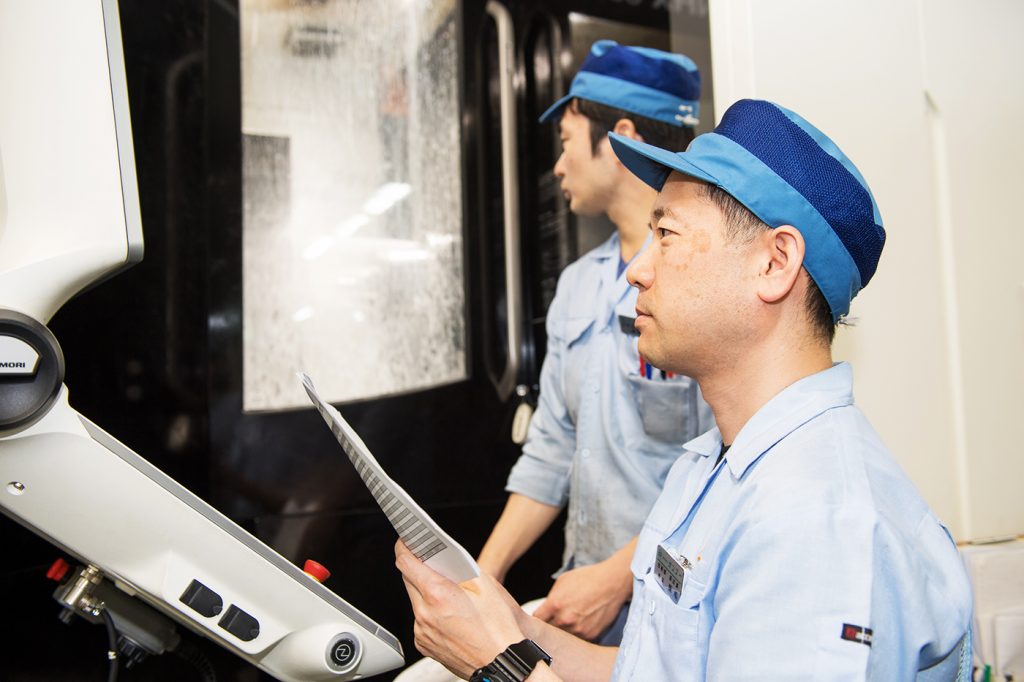
現在はプレス金型の設計が10人、プラスチック金型の設計が6人という体制で業務を行っています。求められるスキルも上がってきているため、現在は3DのCADを駆使して金型設計をしています。ただ、そもそも設計者自体がベテランで経験値の多い人たちなので、かなり複雑な部品が来ても対応できます。その点もサンコーならではの強みだと自負しています。
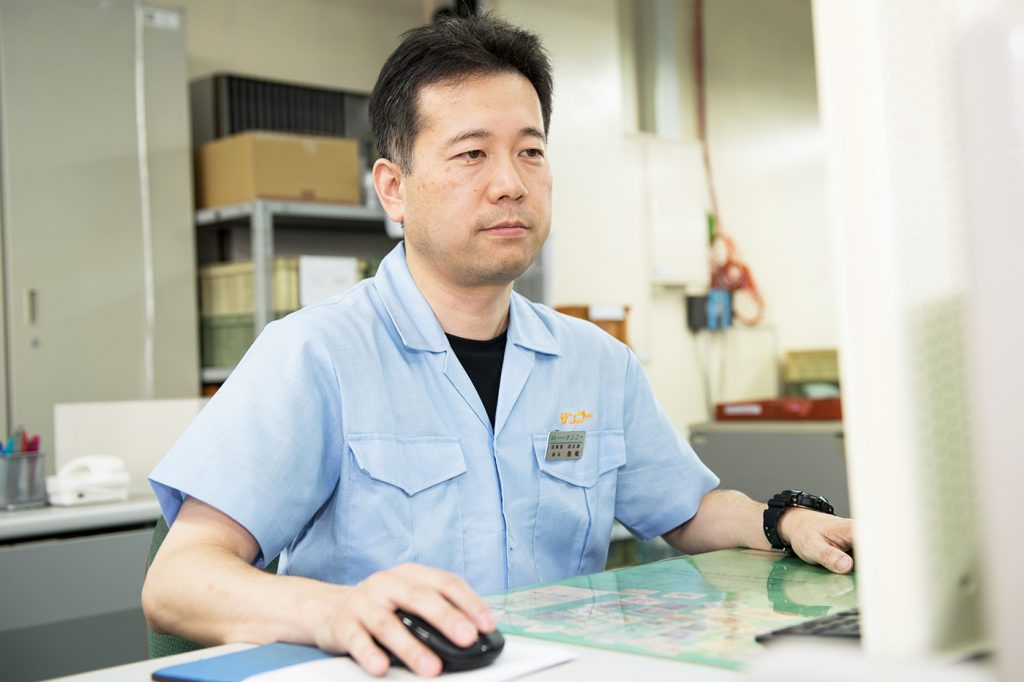
金型設計の上で一番の楽しみややりがいを感じられるのは、やはり自分の設計通りの部品が完成した瞬間。うれしさがこみ上げると同時に、「よかったな」とホッとした気持ちにもなります。あと、お客さまからいただいた図面通りの部品ができるよう金型を設計する――というゴールに至るまでの過程は自由なのです。設計者が10人いれば十人十色で多彩な金型ができるし、「こんなパーツを使って金型をつくりたい」と考え設計すれば実現できるので、それも楽しみの一つ。金型に基本的な構造はありますが、細かい部分に関しては自由度が高くその人の創意工夫やセンス、カラーなどが出てきます。
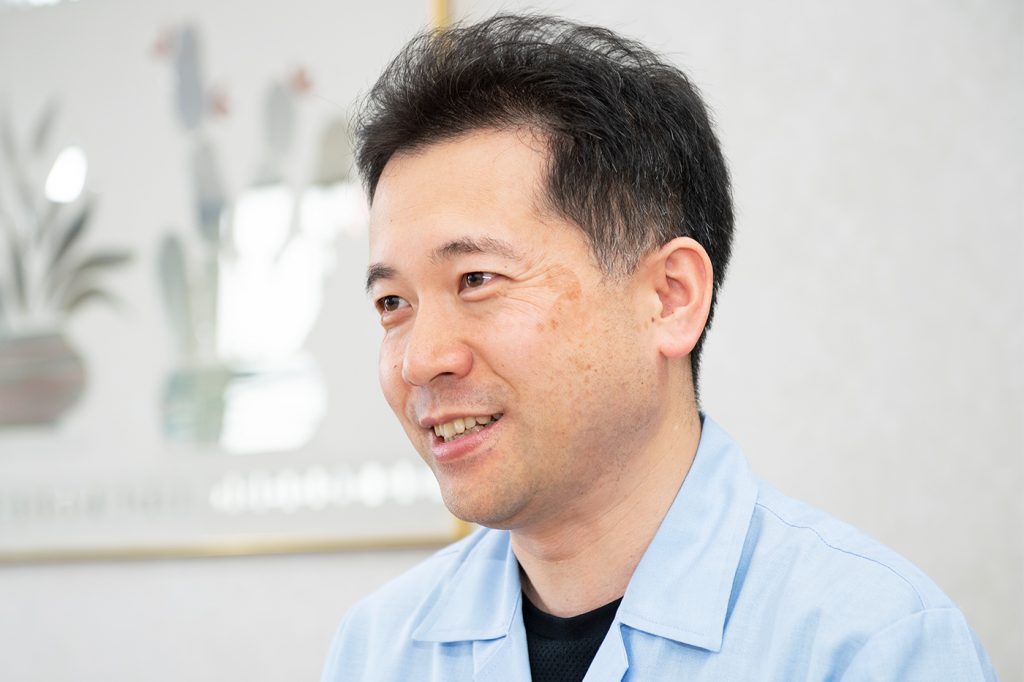
ただもちろん製造サイドの要望もあるので、必ずしも設計した金型の案が100%通るわけではありません。その部分は当然、他部署と調整しながら進めていきますし、うまくいった事例やアイデアなどは課内でも展開して共有します。そうしたサイクルの繰り返しが集積して、金型製作のノウハウや基本的な構造が固まってきています。
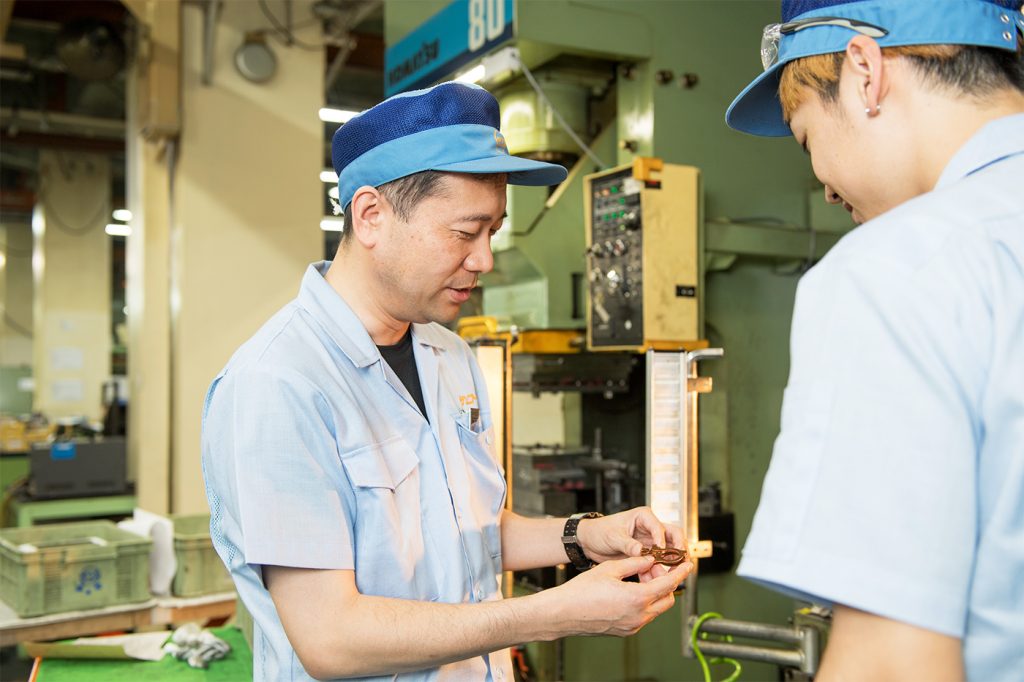
個人的にはもともと、ものづくりに携わりたくてサンコーに入社しました。初めて設計をしたのはずいぶん昔のことですが、昨今のようにIT技術が発達していない時代だったので、紙の図面だけをお客さまにいただき、色々な先輩に聞きながら設計しました。四苦八苦しながら金型をつくり、最終的に初めて製品が出てきたときの感動は今でも忘れられません。それが自分の原点になっています。